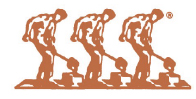
THE MELTMINDER
A PUBLICATION BY BENTON FOUNDRY, INC.
Web Site: www.bentonfoundry.com
BF History Part 8:
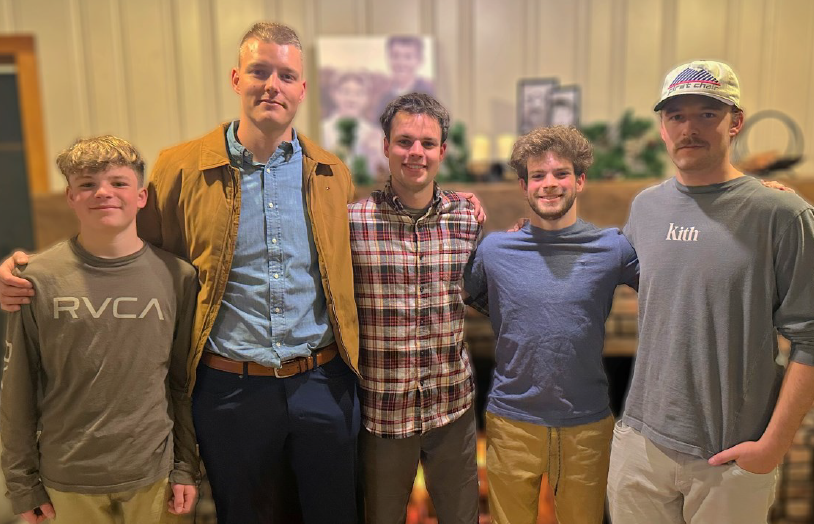
C
ontinual Improvement is a phrase that is overused and underappreciated, but at Benton it is a way of life. The objective is simple…. keep moving forward. Know your starting point. Focus on value. Progress will likely be iterative. Collaborate. Think and work holistically. Keep it simple and practical. Optimize and automate. Repeat.
A foundry is a transportation model. The less you move things, the more efficient you are. Yet, when visiting foundries and other manufacturers, you’ll often find that historical expansions and improvements resulted in a patchwork of buildings and processes. The product does not flow. There are multiple floor elevations, building columns are in the way, etc. Fritz’s view was that if you’re going to invest, then do it the right way. If a column is in the way, then move it. It may cost a bit more up-front, but there is no sense working around it for the rest of your life. The objectives have always been to invest in the plant and equipment to not only increase capacity, but streamline the process, improve process control, and expand your capabilities, while standardizing on the most apropos equipment. Benton Foundry’s facility reflects this mindset. We are in our 9th consecutive five-year capital expenditure plan with over 90% of our profits reinvested during our 45+ year history.
This view and a continual improvement philosophy carries through to other aspects of the operation that have not been previously discussed. Consider the extensive sustainability efforts, including the Benton Foundry Farm, LLC with over 200 acres of managed forest, planting trees to reach carbon neutrality in conjunction with the Pennsylvania Department of Agriculture. Or, consider employee development, with training hours representing roughly 10-12% of all hours worked annually, plus the robust tuition reimbursement program partially funded through a $500,000 endowment at the Pennsylvania College of Technology. As a result of this program, we have an experienced, highly technical staff. Benton Foundry employs over 10 employees with associate’s degrees, over 20 employees with bachelor’s degrees and 7 employees with master’s degrees. In terms of seniority, we have 39 employees with over 20 years of experience PLUS another 40 employees with over 10 years of experience.
The point is that these initiatives are focused on more than just plant and equipment. They relate to sustainability, energy efficiency, information technology, employee development, and succession planning.
This leads us to one of the next exciting steps being taken. Benton Foundry is grooming the next generation. Jeff’s son, Kyle, is the 4th generation and has been with the company for 3-½ years. He has completed a job rotation performing every job in the foundry and is currently on the second shift melt department in a supervisory role. He also recently completed his master’s degree in engineering management from Wilkes University. As the 4th generation, this makes over 100 years that the Hall family has been in the iron foundry industry.
Benton Foundry is not just progress, it’s stability.
Benton Foundry is financially secure, has the technical staff and tools to make complex parts and has equipment and systems that are second to none. And, we continue to think long term as we groom the next generation.
C
ongratulations to Tim Kepner (above), Benton Foundry’s 1st shift Employee of the Quarter and 2024 1st shift Employee of the Year. Tim works in our Production Office as our Traffic Manager. He has held this position since June of 1987. Tim is retiring soon. He lives in Hughesville with his wife, Leslie. Tim has two sons, Korbin and Kyle. He has received this award in the past. Tim is a loyal and dedicated employee. Thank you and Congratulations Tim!
Amazing Job!
C
ongratulations to Stefany Torrealba (below), Benton Foundry’s 2nd shift Employee of the Year. Stefany has been employed at the Foundry since 2022. She currently works in our Melt Department as a Crane Operator. She is a good worker and enjoys learning new responsibilities. Stefany lives in Muncy and she enjoys listening to music, watching movies, cooking, and going to the gym in her spare time. Thank you and Congratulations Stefany!
Awesome Job!
C
ongratulations to Isabella Kubasek (left), Benton Foundry’s 2nd shift Employee of the Quarter. Isabella works in our Quality Department as a QC Assistant. She has been employed since September of 2020, previously working in our core room. Isabella lives in the Benton area. She enjoys listening to music, riding 4-wheelers and spending time with her family and friends when she isn’t working. Thank you and Congratulations Isabella!
Great Job!
A
s an alternative to a Holiday gift for our President, Jeff Hall this year, the office personnel at Benton Foundry decided to donate to a local charity.
Rescue Pets Serving Vets, Inc. is located in Benton, PA just a few miles from Benton Foundry. They are a non-profit organization focused on rescuing shelter pets, abandoned pets and special needs pets. They work on providing necessary medical care, training and love in their foster homes. Their ultimate goal is to home these pets with the right owner, in either the general public or with veterans that need a special companion as a service or emotional support animal.
Volunteer support and tax-deductible contributions enable them to continue to save animals; give them critical medical care, training and eventually the loving homes they deserve. These pets, in turn, help heal the hearts of our veterans, those with special needs and families in our communities.
Here are just a few of their current dogs ready to be adopted or fostered! Check out their website rescuepetsservingvets.org for further details or to make a donation.
D
uring the 4th quarter of 2024, Benton Foundry’s community outreach included the following activities:
-
- Benton Area School District HOSA (Health Occupations Student America) Program – Donor
- Benton Area School District Twenty-First Annual Holiday Meal for Senior Citizens – Donor
- Benton Area School District and Central Columbia High School Spring Sports – Sponsor
- Benton Lions Club Halloween Parade – Donor
- Fishing Creek Watershed Association – Donor
- Northern Columbia County Community Center – Donor
- Wounded Warrior Project – Donor
- Benton Area School District Future Farmers of America – Donor
- Columbia/Montour SWAT Team – Donor
- Penn State University Industrial Engineering Advisory Member
Back Row: Frank Packer (Army), Tom Vandine (Navy), Nick Wilson (Marines)
Front Row: Dave Emmett (Air Force), Eugene Eckroth (Navy), Bill Ferguson (Army)
Back Row: Paul Simko (Army), Kenny O’Brecht (Army), Jim Lamoreaux (Navy), Eric Piatt (Navy), Bob Houser (Army).
Front Row: Dave Hetler (Army), Randy Kadtke (Air Force), Bob Little (Army).
Tim Kepner (Air Force)
Don Copeland (Air Force)
S
cott Stonier of Sweet Valley worked at Benton Foundry for over 28 years (from 1984 until his retirement in 2012). Scott held various jobs at the foundry over the years, machine operator in the core room, molder and in the Pattern Shop. Scott served our country in the US Army during the Vietnam Conflict, earning the Bronze Star. Scott was an avid outdoorsman who enjoyed hunting and fishing. Scott passed on October 9, 2024.
D
avid Thoen, a proud resident of Benton, worked at Benton Foundry for over 30 years (from 1987 until his re-tirement in 2018). The job he held prior to retirement was Setup man in the Core Room. Prior to that he was a Core Machine Operator. David was a staple in the Core Room and was very knowledgeable. David was also a skilled woodworker, avid reader and master storyteller. David passed on October 30, 2024.
WHAT IS REAL ID?
Passed by Congress in 2005, the REAL ID Act enacted the 9/11 Commission’s recommendation that the Federal Government “set standards for the issuance of sources of identification, such as driver’s licenses.” The Act established minimum security standards for state-issued driver’s licenses and identification cards and prohibits certain federal agencies from accepting for official purposes licenses and identification cards from states that do not meet these standards.
These purposes are:
- Accessing certain federal facilities
- Boarding federally regulated commercial aircraft
- Entering nuclear power plants
The deadline for REAL ID enforcement is May 7, 2025.
How do I get a REAL ID?
Visit your state’s driver’s licensing agency website to find out exactly what documentation is required to obtain a REAL ID. At a minimum, you must provide documentation showing: 1) Full Legal Name; 2) Date of Birth; 3) Social Security Number; 4) Two Proofs of Address of Principal Residence; and 5) Lawful Status. States may impose additional requirements, so check with your state’s driver’s licensing agency website, before visiting them in person, for additional guidance and assistance.
Dept. of Homeland Security Website https://www.dhs.gov/
PA Driver’s License with REAL ID (below)
You can visit PennDOT.gov/REALID for more information and a printable document checklist (below).
C
ongratulations to Stuart Wolfe (above) on his recent retirement. Stuart worked at the foundry since 1994. With a degree in Computer Science from Lock Haven, his job duties touched on a variety of departments including, but not limited to, purchasing, payroll and IT. Stuart lives in Hughesville with his wife Mary Megan. They have a son Coleman who lives out of state. Stuart is an active member of his church, is a former Hughesville borough councilman and was involved in Boy Scouting for many years. Stuart and Mary Megan enjoy traveling and visiting NYC for a show on occasion. We thank Stuart for his dedication and service and we wish him a long, happy and healthy retirement!
Congratulations Stu!
We will miss you Stuart and Tim!
Enjoy your retirement
C
ongratulations to Tim Kepner (above) on his upcoming retirement. Tim worked at the foundry since 1987. He was the first Spectrometer Operator. At present, he is Traffic Manager in the Production Control Dept. We thank Tim for getting orders and supplies in and out in a timely manner so production can run smoothly. Tim will likely be spending more time riding his motorcycle and playing golf in the warmer months. We thank Tim for his dedication
and service and we wish him a long, happy and healthy retirement!
Congratulations Tim!
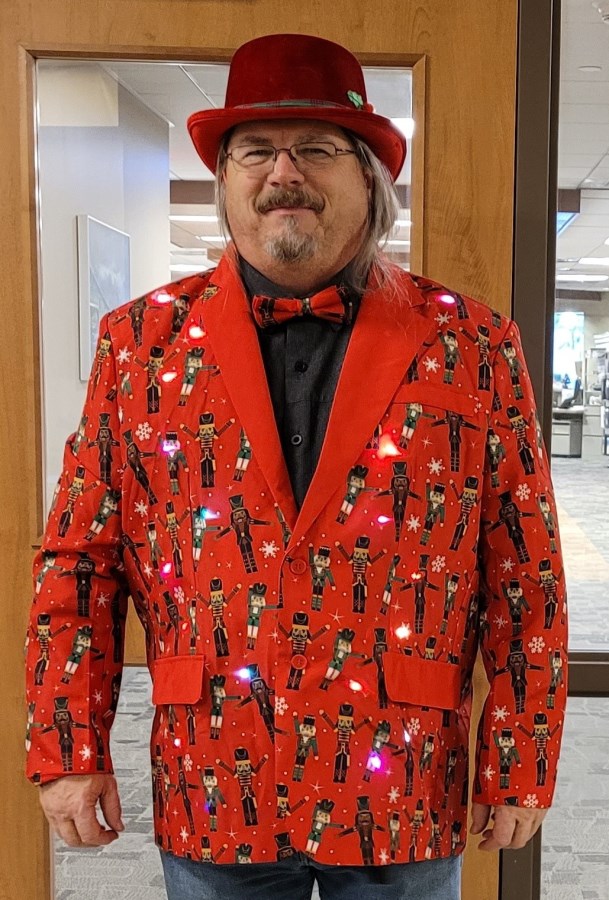
Awesome Job to ALL Employees for our lowest quarterly scrap rate in 4.5 years.
Congratulations to Nick Wilson who graduated with Honors from PCT with an Associate Degree in Automated Manufacturing Technology.
Good Job to Melt and Maintenance on the Furnace 3 coil change. This is scheduled every 5 years as a proactive measure.
Congratulations to Chris Newhart and Mike Parsons for low scrap rates on the Large Disa.
Awesome Job to Maintenance Dept for the lowest Maintenance downtime level in over 3 years.
Congratulations to Kyle Hall who graduated from Wilkes University with a Masters in Engineering Management.
Good Job to Caleb Temple for being among the top five AFS (e-learning) students in the month of October.
Congratulations to Tim Shepherd for Completion of the AFS Introduction to Supervisor Development program.
Awesome Job to Sergio Aguilera and Martha Pineda for continuing their ESL studies.
Good Job to Nick Wilson for a smooth transition to the Maintenance Dept.
Awesome Job to Gilberth Aleman, Jeff Garrison and Chris Newhart for helping Maintenance on non-production days.
Good Job to Timmy Schechterly for continued studies in EET at Penn State, Wilkes-Barre campus.
Congratulations to Ana Ponce, Xenia Ponce and Olin Covington for completion of a course on Casting Defect Analysis.
Good Job to Ryan Keeler for completion of the MAEA Supervisor Leadership program.
Awesome Job to Andy Spencer for filling in as Supervisor for the Night Shift Core Dept .
Congratulations to Morgan Hoover for completion of the Workers’ Compensation Professional course through AMCOMP.
Good Job to Kyle Hall and Cody Snyder for attending the 2024 AFS Melting Conference.
Awesome Job to Bo Boston, Kyle Hall, Ruth Dawson and Caleb Temple for attending Induction training by Inductotherm.
Congratulations to the following personnel for their 4th Quarter 2024 performance.
Cindy Newhart – Highest Core Production Efficiency
Myriam Mayorga – Highest Core Assembly Efficiency
David Straub – Highest Molding Efficiency
Tom Foust – Lowest Molding Scrap Rate
Eric Barnes – Highest Grinding Efficiency
Sergio Aguilera – Highest Foxall Running Time
K
udos to our Lab for once again scoring well in the Iron Casting Research Institute’s (ICRI) round 55 Spectrometer Proficiency Testing. Benton Foundry’s Lab once again showed no statistically significant differences for repeatability and reproducibility. This testing measures repeatability and consistency between various technicians within a lab and reproducibility and consistency between different labs. Our Lab has continually been recognized for consistently high performance in these exercises. Thanks to Jackie Showers, Cody Snyder, Xenia Ponce, Isabella Kubasek, Bill Simback, Elizabeth Strauch, Jenifer Rundle and Ramiro Pomares.
- Milton Hershey introduced Hershey’s Kisses in 1907.
- Until 1921, each Kiss was wrapped by hand.
- The Hershey Company produces over 80 million Hershey’s Kisses per day. This is about 60,000 Hershey’s Kisses every minute.
- The machines that wrap Hershey’s Kisses can wrap up to 1,300 chocolates per minute.
- The aluminum foil used to wrap Hershey’s Kisses is recyclable.
- Hershey’s Kisses are one of the most popular chocolate candies in the United States.
- The paper plume on top of each Kiss was added in 1921 to distinguish Kisses from other candies.
The Hershey Company’s machines run 24 hours a day, seven days a week.
- The name “Kisses” may come from the sound of the machine dropping the Kisses onto the conveyor belt.
~ AI Overview
T
he story of Maine’s native wild turkeys is one of triumphant recovery following extirpation in the early 1800s. We are thankful for successful reintroduction in the 1980s and the healthy population we have today.
- Wild turkeys have numerous distinct vocalizations beyond gobble gobble. Their vocabulary includes cackles, clucks, purrs, putts and more!
- Wild turkeys are impressive triathletes. They can run 18 miles per hour on foot, fly nearly 60 miles per hour for a short sprint and are surprisingly powerful swimmers!
- The bare head and neck of a wild turkey are composed of a wattle, caruncles and a snood that expands, contracts and changes color with their mood!
It takes more than a single handprint to draw a wild turkey. There can be over 5,000 feathers on a single bird!
- Young turkeys are called “poults.”
- You can tell the sex of the turkey by the shape of their scat—female scat is curly and male scat is a “J” shape.
~ mefishwildlife.com
T
hey provide us with comfort, but sometimes they need it too. Before he recently passed, my husband would tell me how much he loved the two of us. Meaning me and Maple, our dog. He and Maple were inseparable. Even as Jerry lay on a hospital bed we had placed in our family room, Maple would pop up and lick him. That made Jerry smile when he had little to smile about in the throes of Lewy body dementia.
After Jerry died, Maple wasn’t interested in things she used to love, such as toys and food. Like me, she was suffering from grief. How could I help Maple?
Kathryn Dench, chief veterinary advisor at Paw Origins, which sells pet supplements online, offers tips:
- Maintain normalcy. Routine is key. Keep walks and feedings consistent.
- Provide extra attention. Give your pet more cuddles and pats.
- Socialize. Interaction with other dogs and people can lift spirits.
Maple is doing much better. Each morning at 7am she licks my face, reminding me that she’s hungry and wants love. Now we are the two-some.
~ Judy Mandell
~ AARP The Magazine
Elissa Romberger
Jim Tumolo
Glenda Chavez
Scott Vandine
Randy Kadtke
Boane Berg
Shawn Frey
Fred Hittle
Joseling Martinez
Gene Ryman
Mark Coleman
Marty Pelas
Kenny O’Brecht
Colton Young
Matt Shultz
Mike Shultz
Eric Barnes
Joe Sharkuski
Oscar Aguilar
Harry Fry
Mike Modla
Jeff Jones
Kris Young
Olin Covington
Lynn Sheatler
Joe Timko
Nate Foust
Erick Tellez
John Andrews
Tom Foust
Greg Vandine
Ryan Keeler
Tim Shepherd
David Straub, Sr.
Sherry Nerio
Olivia Schechterly
Mike Machuga
Chris Madl
Katherine Miron
Gerson Urbina
Francisco Rocha
Bob Little
Della Norton
Annette Brown
Ed Whitmoyer
Justin Boyer
Andy Spencer
Mike Schumacher
Gilberth Aleman
Carlos Tellez
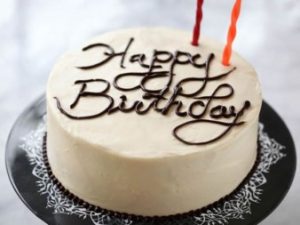
What country produces the most iron ore?
Answer will be in 1st Quarter 2025.
Can you identify five different industries that you will find our products in?
Food Processing Equipment, Steam Products, Municipal Applications, Sprinkler System Components, Water and Wastewater Processing Equipment, Heating, Ventilation and Air Conditioning Equipment, Industrial Washing Machines, Agricultural Applications, Power Generation and Distribution, Oil and Gas Processing and Distribution, Munitions, Mining, Marine, Excavation, Road Construction, Railroad, Fluid Power, Motors, Bearing and Drives, Cranes, Hoist and other Material Handling Equipment, Pumps, Valves and Meters
Daily Writing Tips
“Whenever you see a successful business, someone once made a courageous decision.”
~Peter F. Drucker